Research
- CASA's research is structured in 7 different Work Packages -
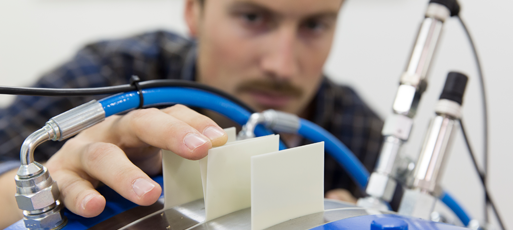
Metallic Materials
Constitutive models describe the stress and internal variables (representing in an average sense the microstructural rearrangements of the material) as function of the strain, strain rate and temperature. In large-scale simulations of structures, the framework of continuum thermo-mechanics is typically adopted to formulate the constitutive models, while thermo-mechanical testing is used to identify the model parameters.
Advanced constitutive models, including plastic anisotropy, non-linear isotropic and kinematic hardening, strain-rate and temperature dependence, damage evolution and failure, tend to have a large number of model parameters. This programme is designed to apply multi-scale methods for constitutive modelling in a top-down/bottom-up methodology for large-scale numerical simulations of metal structures. This will reduce the need for calibration to thermo-mechanical tests and improve the prediction accuracy with respect to properties that are not always easily measured by testing. Qualitative and quantitative descriptions at different length scales will be closely accompanied by well-designed experiments at the length scales of relevance for the phenomena of interest (from the nano-scale to the complete structure), as a basis for achieving improved understanding, model developments and model validation.
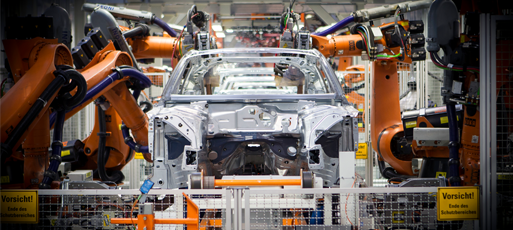
Industrial Implementation
In order to strengthen the industrial implementation of the research and cooperation between the partners, an industrial reference group has been established where there is one expert from each partner. The mandate of the industrial reference group states that an annual report has to be presented to the SFI CASA Board about how the implementation is carried out. A survey has been completed to facilitate the interaction between the research group and the partners with respect to implementation. The partners were asked to define what implementation means, how implementation was carried out and how the partners disseminated the obtained results in their own organization. In addition, the partners have been asked to define what is within and beyond the scope of the Centre and how they define an active partner or a partner who only follows the research activities. The answers from the partners show that implementation is defined as short- and long-term activities. In a short-term perspective, a key issue is the training of the partners to use the tools that are developed, whereas for long-term activities they expect that the technology will be implemented into their daily processes. Implementation in such processes means for instance that the models developed are incorporated into the commercial solvers used by the partners and that the models are robust, accurate, user friendly and well documented. All implementation in the Centre starts with the proof of technology through master’s projects at NTNU linked to the Centre’s activities.
The partners launch the topic of the master’s projects through the industrial reference group. At a later stage, an internal evaluation of the technology is carried out by the partners hosting master’s students. PhD candidates can also contribute here. The proof of technology and the internal evaluation are within the scope of the Centre, whereas concurrent projects are outside. All implementation is followed by training courses at NTNU or at the partners. These courses are linked to a validation strategy on several scales.
Methods and Tools
The Methods & Tools programme provides a synthesis of the research carried out to facilitate industrial implementation. It consists of three main parts: further development of the SIMLab Toolbox, development of guidelines for best practice, and training and education of students and engineers. The SIMLab Toolbox is further developed by enhancing the prediction accuracy, efficiency and robustness of existing models and methods.
The appropriate tools at different scales have to be developed in order to assist the research in the other CASA programmes. In particular, the SIMLab Toolbox supports the necessary steps to build a reliable finite element model for advanced structural analysis, including: a database solution to store and get access to experimental data and protocols; a field measurement software to extract accurate data from tests; a multi-scale calibration toolbox to identify the parameters of the proposed models; a model library with constitutive models for the different materials used by the partners; a set of multi-scale solvers used to develop and improve existing models. The SIMLab Toolbox is linked to the finite element codes used by the partners through an interface. Industrial methods are established for verification and validation of the developed experimental and numerical methods at different scales. Recommended practice are developed for the use of advanced computational methods (e.g. non-linear finite element methods) to determine the characteristic resistance of structures. In large-scale numerical simulations, the predicted behaviour of the structure - and thus the structural resistance - is a function of several factors, such as the behaviour and modelling of the material at different temperatures and loading rates, the modelling of joints, the spatial discretization of the structure, and the modelling of boundary conditions and loads. Another issue here is the representation of aleatory and epistemic uncertainties in the numerical simulations. The modelling of the structure has to robustly capture the potential failure modes of the members, the joints and the structural assembly. Modelling guidelines are developed for cases where there is no overlap between the validation domain and the application domain. The recommended practice activity is based on the relevant design codes for steel, aluminium and offshore structures, i.e. EC3¹, EC9² and NORSOK³, respectively. The programme also provides training of master’s students in addition to engineers and scientists at the user partners. The training of master’s students is achieved through advanced courses and thesis work closely connected to the research activities in CASA. The training of engineers and scientists at the user partners is achieved by targeted training courses and workshops.
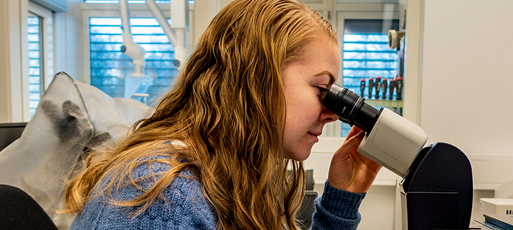
Lower Scale
This programme concentrates on the lower length scales of materials, from atomic up to micrometre scale, and will provide experimental and calculated input to the multi-scale framework and constitutive models from the lower scale. This will provide input for microstructure evolution, strength and work hardening for metallic materials, such as aluminium and steels, and a foundation for development of physically based models for crystal plasticity, continuum plasticity, damage and fracture.
Advanced constitutive models, including plastic anisotropy, non-linear isotropic and kinematic hardening, strain-rate and temperature dependence, damage evolution and failure, tend to have a large number of model parameters, some of which need to be taken from a lower scale.
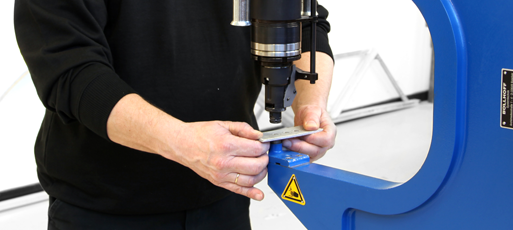
Structural Joints
Multi-material joining techniques are becoming increasingly important and have applications in a wide variety of industries from oil and gas, physical security, automotive, aerospace, and energy systems to consumer goods and medical devices. The demands for improved system performance, weight reduction and reduction in manufacturing operations for components and structures are increasing. To meet these demands, materials with a high strength-to-weight ratio are becoming increasingly attractive and the joining of these materials presents challenges.
Traditional welding techniques are not capable of joining materials that are dissimilar in nature (e.g. metals to polymers). Thus, joining technologies such as adhesive bonding and mechanical fastening have to be considered to accommodate these challenges and enable more widespread use of multi-materials in structures. The advancement of joining technologies is critical to expand the use of new multi-material assemblies. Currently, process modelling and the simulation of multi-material joining techniques are not ready for industrial applications and the mechanical properties of complex joined structures cannot be predicted. Research on different physical scales is required to obtain a more fundamental understanding of deformation, damage and fracture, and other failure mechanisms. In the design of structures or products, large shell elements are used for computational efficiency which hampers an accurate representation of the connections and their failure modes. Engineering approaches that increase the prediction accuracy, but do not affect the overall computational time have to be developed based on a fundamental understanding of the behaviour of the structural joint.
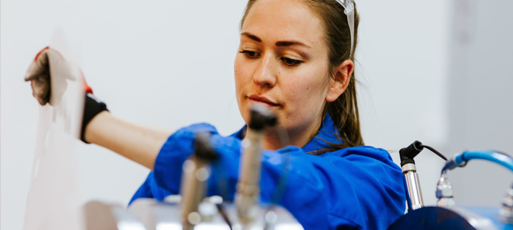
Structures
Design against accidental loads, such as explosions, impacts and collisions, has become increasingly important for a number of engineering and industrial applications. To meet the challenges posed by such complex loading conditions, product development and structural analysis are increasingly carried out in virtual environments using the finite element method to achieve safer and more cost-effective designs.
The fundamental goal of protective structures is to improve the survivability of people and vital infrastructure to a given threat. It is important to realize that the protective structure is the last layer of defence against a threat when all other protective measures have failed. It is thus of utmost importance that such structures are designed and validated on a sound theoretical and experimental basis. To do so, accurate, efficient and robust constitutive models and solution techniques used in a multi-scale modelling context are required. Further, new designs need to be validated through high-precision experiments involving advanced instrumentation such as three-dimensional digital image correlation for full-field displacement and strain measurements. Although much information can be obtained from laboratory tests, relying on such an approach would be too costly and inefficient. Computer-aided design, together with a strategy for material selection, optimization and well-selected validation tests, can significantly lower the cost and enhance the overall quality and efficiency of the required protection.
Polymeric Materials
Polymers comprise a wide range of materials, including natural and synthetic materials. The demand for such materials has increased considerably during the last few decades. Applications include, but are not limited to, safety-related parts in cars, coatings, thermal insulation in offshore components, seals and inter-glass layers in laminated windows. The finite element method has only recently been employed as a tool in the design process of parts made of polymers. Therefore, constitutive models for such materials are less mature than for metals. Also for polymers, knowledge about the physical mechanisms governing the thermo-mechanical behaviour is of utmost importance for successful development of constitutive models.
The research programme will pay attention to elastomers, commodity thermoplastics (like PE and PP), fibre-reinforced thermoplastics and foams made of polymers. Typically, polymers made for commercial purposes contain mineral or rubber particles. Some material models for polymers have been implemented in the SIMLab Tool Box, but the validation process has been limited to constitutive models for ductile thermoplastics. Other research groups have also worked on material modelling for polymers. The literature reveals, however, that a majority of the proposed models involve a rather high number of material parameters, rendering the parameter identification from experimental tests more difficult. Industrial application of a material model usually demands that the calibration of the parameters is straightforward. Prediction of fracture is also a topic of interest for research and industry. The accuracy of fracture criteria is closely related to the quality of the constitutive model because it is essential to have an adequate description of the evolution of stresses, strains and other internal variables during the thermo-mechanical history of the part under consideration.