News - Metal Production
News
Congratulations Dr. Hoover!
Haley Hoover successfully defended her thesis "Electrical Resistivity of Materials in the Silicon Furnace" September 26th 2023. The topic of Haley's presentation at the trial lecture was “Quantitative and qualitative environmental impacts of the international ferroalloy industry”.
Congratulations dr. Arnesen!
Kamilla Arnesen successfully defended her thesis "PAH emissions from the metallurgical industry" September 5th 2023. The topic of Kamilla's presentation at the trial lecture was “Airborne emissions from the Norwegian oil- and gas industry - state of the art and future perspectives”.
Eight years of research on metal production – what have we learned?
SFI Metal Production started the centre activities in April 2015. In 2023 the eight years centre period comes to an end, and it’s time to summarize the results, impact and innovations that have been produced during the centre period. The final Centre Meeting took place at Nidelven Hotel in Trondheim April 25th-26th, and more than 80 attendees from research- and industry partners participated.

The TMS 2023 Annual Meeting & Exhibition
The TMS 2023 152nd Annual Meeting and Exhibition was successfully held March 19-23 in San Diego in California with more than 3500 participants. During the 5 days conference, representatives from both NTNU and SINTEF gave talks and presented their work.

Green production of silicon is just around the corner
Researcher Maria Wallin and Professor Gabriella Tranell at NTNU, department of Materials Science and Engineering co-coordinate the large EU projects SisAl Pilot and SisAl Slag.
NTNU has taken out a patent for an industrial process that will remove all direct emissions of CO2 and NOx. The process has been named SisAl.
With today’s technology, CO2 is formed when quartz reacts with carbon. Instead of carbon, the SisAl process uses aluminium as a reducing agent, thus avoiding the formation of CO2.
Twenty-two partners in research and industry in Europe and South Africa have developed the process based on NTNU’s patent. You can read more about the project in this recently published article.
Congratulations Dr. Gylver
Sindre Engzelius Gylver successfully defended his thesis january 20th 2023. The topic of Sindre's presentation at the trial lecture was “Flue-gas Recycling in the Al-industry - Challenges and Opportunities”. The trial lecture was followed by an excellent presentation of his PhD thesis “Feeding of Alumina in Molten Cryolite Bath”.
Congratulations Dr. Hassanabadi
Dr. Massoud Hassanabadi successfully defended his thesis December 16th 2022. The topic of Massoud's presentation at the trial lecture was “Inclusion removal by degassing: Industrial practice and outlook”. The trial lecture was followed by an excellent presentation of his PhD thesis “Characterisation of Alumina Based Ceramic Foam Filters (CFFs) – An Experimental and Modelling Approach”.

Congratulations Dr. Billy
Dr. Romain Billy successfully defended his thesis December 15th 2022. The topic of Romain's presentation at the trial lecture was “Novel aluminium manufacturing processes and alloys and their impact on absorption of end-of-life scrap”. The trial lecture was followed by an excellent presentation of his PhD thesis “Monitoring and simulating material cycles and emissions at multiple scales - Case studies for aluminium”.

Congratulations Dr. Solem
Dr. Cathrine Kyung Won Solem successfully defended her thesis November17th. The topic of Cathrine’s presentation at the trial lecture was “Use of Ionic Liquid Solvents for Metal Recovery”. The trial lecture was followed by an excellent presentation of her PhD thesis “Parametric Study of Molten Aluminium Oxidation in Relation to Dross Formation at Laboratory and Industrial Scale”.
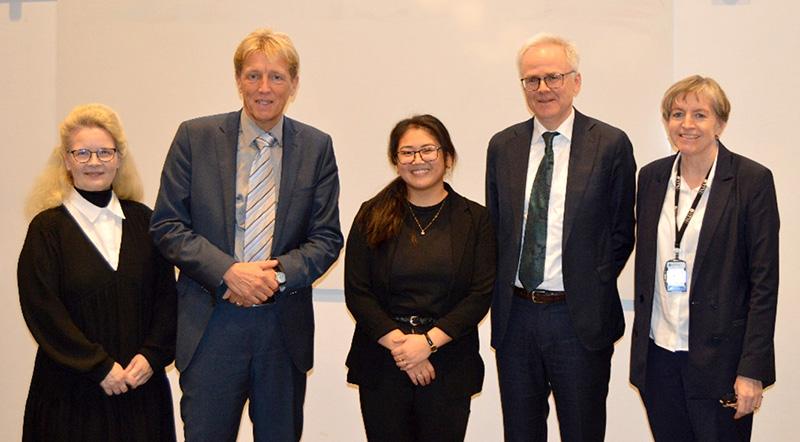
SFI Metal Production Autumn Meeting and Symposium in honor of Professor Leiv Kolbeinsen
November 1st SFI Metal Production organized the Autumn Meeting for all centre members. This was followed by an all-day symposium in honor of Professor Leiv Kolbeinsen November 2nd.
The SFI Autumn meeting focused on Highlights from the centre period, and representatives from industry and the SFI research organizations gave presentations.

Successful THANOS conference in Johannesburg
September 28th- 29th the International conference on Enhanced use of Thermodynamic Data in Pyrometallurgy Teaching and Research was organized in Johannesburg, South Africa. The broad objective of the conference is to enhance the use of thermodynamic data in pyrometallurgy teaching and research.
Refining and Recycling of Metals seminar
The Refining and Recycling of Metals seminar was arranged at Britannia hotel, the 5th and 6th of September. The seminar was arranged in order to celebrate the publishing of the book of the same name.

The main author, Thorvald Abel Engh, was a guest of honour together with Christian Simensen and Olle Wiik, who had both written important chapters. There were also very interesting presentations from Trond Furu, Sarina Bao, Martin Syvertsen, Eivind Øvrelid, Aud Wærnes, Otto Lunder and Anne Kvithyld. John Grandfield gave a pre-recorded presentation, as did one of the book’s main contributors, Geoffrey Sigworth, who gave a humorous and interesting retrospective. The seminar was streamed online, and 50 people participated.
We would especially like to thank Ingrid Page for organizing a successful seminar!

The Silicon for the Chemical and Solar Industry Conference June 14th-16th
The Silicon for the Chemical and Solar Industry was organized June 14th -16th as an online conference. The aim of the conference was to discuss new development in silicon process technology, silicon quality assessment and performance in the subsequent chemical reactions including resource, energy and environmental issues. Silicon producers as well as users and academia were invited to attend.
Aluminium (CaNAl) Summer School June 14th -16th
A summer school on aluminium was organized at Gløshaugen campus (and Zoom) June 14th-16th. The summer school was part of the INTPART project CaNAl, which aims to promote and facilitate joint research and education related to aluminum between Canada and Norway.

Successful SFI Spring Meeting April 26th-27th
The SFI Metal Production spring meeting was held in Trondheim April 26th - 27th. 55 participants from industry and academia met at Lerkendal Hotel for a two-day-meeting.

Sindre Gylver participated at PhD Grand Prix
March 28th PhD candidate Sindre Gylver participated at PhD Grand prix in Trondheim. This is a dissemination contest hosted by the student organization for Chemical Engineering at NTNU.

In this contest, PhD Candidates from several departments at the Faculty of Natural Sciences compete on explaining their research in an understandable and entertaining way. This is an excellent opportunity for PhD candidates to practice and demonstrate their dissemination skills, in addition to promote the career as a PhD Candidate for relevant students.
Congratulations to Sindre who made an excellent presentation at the PhD Grand Prix!
TMS 2022 Annual Meeting & Exhibition
The TMS 2022 150th Annual Meeting and Exhibition conference, Furnace Tapping 2022 and REWAS 2022 were all co-located and organized in Anaheim, California from February 27th to March 3rd. NTNU and SINTEF were represented in all three conferences with more than 30 researchers and master students.

Bellona seminar 2022: Charcoal - an important climate solution
February 7th 2022, the Norwegian Ferroalloy Producers Research Association (FFF), together with NTNU and SINTEF, participated in Bellona's mini-seminar «Charcoal - an important climate solution».

Invited guests were Minister of Climate and Environment Espen Barth Eide and representatives of Stortinget’s energy and environment committee, as well as the industry committee. Bellona presented the report "Biocarbon as a climate solution in industry" to the Minister of Climate and Environment.
30 people from 10 different companies at the Gas Purging of Metals Seminar
The Gas Purging of Metals Seminar, held on Thursday the 17th of February, had a good turn out with 30 people.
10 different companies attended: Elkem, Eramet, Wacker, Hydro, Hycast, Alcoa, Reel alloys, GKS Engineering Services, SINTEF and NTNU. The seminar gave background theory for refining of molten metals with practical examples from aluminium, silicon and steel. Instructors were: Geoffrey K. Sigworth, GKS Engineering Services, Arild Håkonsen, Hycast and Erlend Lunnan Bjørnstad, Elkem.
Thank you to the instructors and attendees for after work hours!
Exchange student from South Africa to SFI Metal Production
Jamey Davies is the first exchange student in SFI metal Production and the Intpart project Thanos since Covid started. It is hence with great pleasure we wish her welcome to NTNU for 6 months.
Jamey Davies is on her second MSc -year at North West University in South Africa. She is investigating the prereduction of FeCr ore with H2 and has so far published 2 journal papers in this topic.
During her stay in Trondheim, she will investigate the prereduction of Mn-ores with H2. She will work closely with the Reduced CO2- and the Prema-project, and will hence investigate complementary ores.
You can meet Jamey in her office in the SFI area, 3rd floor, Bergbygget.
Welcome to SFI Metal Production!
Tizir receives 261 mill NOK from ENOVA to substitute fossile reductants with hydrogen
Congratulations to Tizir and KPN Reduced CO2 with the ENOVA funding to this important and ambitious project!
KPN Reduced CO2 is investigating the possibility to substitute fossile reductants with hydrogen in metallurgical processes including ilmenite production. This is now one step closer to industrialisation. The Norwegian ilmenite upgrader, TiZir ,one of the partners i KPN Reduced CO2 have now recieved 261 mill. NOK in support from ENOVA to build a pilot and demonstration plant for pretreatment of ilmenite by hydrogen.
Funding from RCN to strategically important infrastructure
SINTEF and NTNU have received funding from the Research Council for laboratory equipment related to Metal Production and Recycling. The equipment will enable advanced research in both pyro-, hydro- and electrochemical production.
The primary objective of the investment is to provide laboratory equipment supporting research in the transition to green, circular and sustainable metallurgy. SINTEF, with Dr Arne Petter Ratvik is the project owner and Professor Gabriella Tranell, co-director at SFI Metal Production, is leading the project from the NTNU side.
-We are very pleased with the awards from the Research Council. With this funding we are one step closer to transition to green, circular and sustainable metallurgy! The proposed infrastructure will expand upon existing infrastructure at NTNU and SINTEF.
New book: Principles of Metal Refining and Recycling
Congratulations to SFI research area leader Anne Kvithyld with the publication of the book Principles of Metal Refining and Recycling. The book provides a self-contained introduction to the field of purification and recycling of metals.
The scientific principles in the treatment of the various metals are the same. The importance of using a clean and properly alloyed metal is described in detail. The text covers thermodynamics, physical and transport properties, mixing, mass transfer and numerical models. It describes methods for removal of dissolved impurity elements, particles, and inclusions. It considers important aspects of the solidification process, remelting and adding of alloys. Recycling, future challenges and specific processes for each metal are discussed in detail.
Authors are Thorvald Abel Engh (NTNU), Geoffrey Sigworth (GKS engineering) and Anne Kvithyld (SINTEF), and the work has been partly funded by SFI Metal Production. The book is a greatly extended update of the 1992 book Principles of Metal Refining by T. A. Engh. It includes in particular the subjects of metal recycling, ferrous and non-ferrous metal refining, and metalloids like silicon.
New Elkem project aims to eliminate CO2 emissions from silicon production
The Research Council of Norway has granted Elkem NOK 16 million to develop a new concept for silicon production where all direct CO2 emissions are eliminated. This may become a game changer for the global silicon industry. Elkem already uses 83% renewable electricity in its operations and aims to be part of the solution to combat climate change. Silicon is a critical material for digital technologies and the green transition.
The project will run from 2022-2024. Elkem is project owner and Aasgeir Valderhaug is project manager. The Norwegian R&D institutes SINTEF and NORCE, and the pilot test centre Future Materials, will be research partners. Senior research scientist Eli Ringdalen participates in the project from SFI Metal Production.
Successful SFI Autumn Meeting November 2nd-3rd
The SFI Metal Production autumn meeting was held in Trondheim November 2-3. Due to the corona virus situation, we have not been able to organize physical consortium meetings the last two years. This time we could invite to a hybrid meeting, and about 50 participants from industry and academia met physically at Royal Garden Hotel. In addition 40 participants attended the meeting online.
Successful INFACON Conference
The 16th International Ferro-alloy Congress – INFACON XVI - was arranged as a digital conference on the 27th to 29th September from Trondheim. The intention of INFACON is to stimulate technical interchange on all aspects of silicon/ferroalloy production. The vision for the three-day conference was "CO2 free ferroalloy production". The presentations reflected the vision with a major focus on decreasing CO2 emissions, clean technologies, recycling including energy efficiency, modelling, emissions (reduce the PAH exposure risk etc.) and Markets.
Elkem Award to Professor Gabriella Tranell
Congratulations to Professor Gabriella Tranell for receiving the special award from Elkems Research Fund. The winner of the award was presented 28 September, 2021 at the opening of the INFACON XVI conference. Tranell receives the award because of her broad research and contribution to the Ferrosilicon/Silicon industry.
Congratulations Dr. Lunnan Bjørnstad
Dr. Erlend Lunnan Bjørnstad successfully defended his thesis August 18th. Erlend did an excellent presentation at the trial lecture: “Electrolytic production and refining of silicon, fundamentals and state of the art " followed by the presentation of his PhD thesis “Oxidative Ladle Refining of Metallurgical Grade Silicon: Refining of Ca and Al Impurities”.

Unwanted material on solid surfaces
Daniel Clos at SFI Metal Production defended his thesis in May 2021. In this blog he presents the main results from his important research on "Formation of Hard Grey Scale (HGS) on the Surface of a Cold-finger in the Aluminium Production Industry".
Congratulations Dr. Clos!
Dr. Daniel Perez Clos successfully defended his thesis May 26th. Daniel did an excellent presentation of the trial lecture: “Mechanisms of ash transport and adhesion on cylindrical tubes in crossflow" followed by the presentation of his PhD thesis “Formation of Hard Grey Scale (HGS) on the Surface of a Cold-finger in the Aluminium Production Industry”.
